Manufacturing 40 Years ago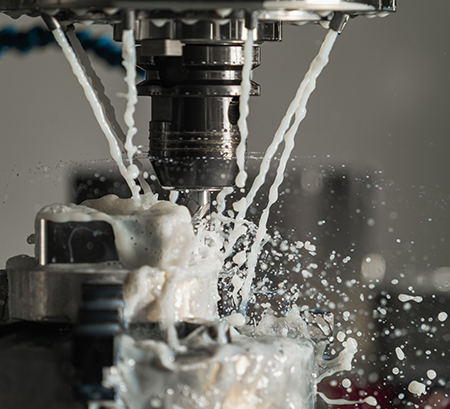
Back in the late 70’s, I started my career at Grumman Aerospace and we had all NC (Numerical Control) machines in our plants as well as the very first licenses of Catia ever used in the U.S. ‘CNC’ (Computerized Numerical Control) technology was extremely new and had not yet made its way to our plant.
Our machines to manufacture parts had no memory and were driven by mylar or paper tapes that had G-Code programs punched into them. Longer programs simply were made up of longer tapes. The NC machine read the tape and simultaneously ran the program. If the tape tore, a new one was punched. NC machines were extremely expensive and well out of reach for most small to mid-sized job shops and manufacturers.
There was no ability to edit programs at the controller and no ability to store multiple programs on a controller. If there was an error in the program, it meant scrapping the tape (and possibly the part) and starting all over. Programmers of NC machines were referred to as ‘NC Programmers’ and likewise, we also had ‘NC Operators’.
In the early 1980s, CNC machines began showing up at Grumman. The need to punch mylar or paper tapes was no longer required. DNC (Distributed Numerical Control) systems came to fruition and we could transfer programs to the CNC’s through a proprietary shop floor network. CNC controllers had memory to store multiple programs as well as edit them. Operators could ‘dry run’ (test) programs, block by block, without needing to keep rewinding the tape…
For those of you who are G-Code enthusiasts, an ‘M30’ isn’t officially an ‘End of Program’, as many think. That’s actually an ‘M02’. An ‘M30’ is a ‘Rewind Tape’ command, signaling the NC machine to rewind the tape to the beginning to run the next part.
CNC machines were now available and in the mid to late 1980s, pricing was becoming more affordable for some smaller CNC machines. Additionally, Personal Computing power became available to the masses in the form of ‘386-based computers’ thus enabling affordable CAM software to be developed and perfected to take advantage of the more powerful computers and video technology.
In the 1990s and into the 21st century, given the expansion in capabilities and affordability of part programming software and CNC machinery along with continuous computing growth, there was a huge boom in job shops springing up with CNC equipment and CAM programming software.
CNC machining, where material is removed from billets, castings, and forgings to produce final parts is today referred to as ‘Subtractive Manufacturing’ in order to distinguish it from our newest player, to be discussed shortly, called 3D Printing or ‘Ádditive Manufacturing’.
Much like NC programming, the technology originally known as Stereolithography that arose in the 1980s was extremely expensive and out of financial reach for most. But machines running this fascinating technology to start with a vat of photo-curable polymer and use lasers to cure different levels of the material to form parts was absolutely incredible and those with good technological vision could see what was coming.
Manufacturing Today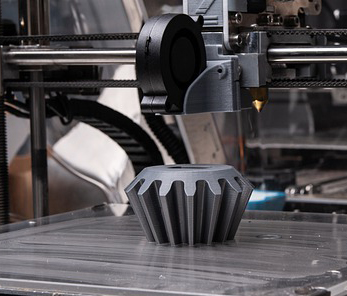
CNC equipment, even elaborate multiaxis mills, lathes, mill/turns, routers, contour lasers, punch presses, EDM’s, grinders, and the like are used in tens of thousands of shops. Price-point and accuracy become more attractive as each year passes. As computing power increases and software is modified to take advantage, the speed and capabilities of CNC’s have grown to tremendous heights. CNC Programming went from 6-figure investments in software and workstations prior to the days of 386-based Personal Computing to being extremely affordable today, running on personal computers. Stereolithography machines of the early ’80s were $750K – $1.5 million to purchase, very limited on geometric shapes, size, resolution, material, and accuracy, and were not a practical investment for most manufacturing companies. 3D Printers of today, however, are much more accurate, hold higher resolution to achieve far better surface finishes, use a variety of materials and technologies including the printing of metals and composites, and are affordable to many manufacturers and even hobbyists.
Today, some of the more innovative CNC manufacturers are beginning to develop hybrid machines such as the Lasertec 65 that can ‘grow’ models (using Additive Mfg.) in 5-axis as well as turn and mill parts in 5-axis mode (Subtractive Mfg.). Additionally, new CAD design companies have emerged to take advantage of the Additive Design process and CAM software manufacturers are starting to consider programming for hybrid machines that perform both Additive and Subtractive manufacturing. But machines like this today are well out of reach financially from most manufacturing companies. Does this sound familiar?
What Will Manufacturing Look Like 40 Years From Now, or Even Sooner?
What will manufacturing look like in the year 2060? Well, I’ll be 100 years old and perhaps will be starting to think about retirement, but if history has anything to say about it, hybrid machines that can perform both Additive and Subtractive manufacturing will be commonplace and affordable. Every machine will be able to ‘grow’ and ‘machine’ parts and assemblies of varying materials. In fact, the idea of designing ‘mechanical assemblies’ may disappear completely as they only really exist today due to current manufacturing limitations.
Printing will be used where it can produce optimal parts and Subtractive Manufacturing isn’t possible and perhaps Subtractive will be used where extreme accuracy is required or to machine features that are more difficult to ‘grow’. All design and manufacturing software will need to offer tools for both Additive and Subtractive operations. Some of the larger CAM suppliers of today are beginning to explore what programming for Additive Manufacturing will mean and how it will tie into traditional (Subtractive) manufacturing. I suspect all future CAM suppliers will address both Additive and Subtractive technologies within the same software. More than likely, analysis technology will be built into the software, providing ‘tips’ to the designer as to which materials to use for the application(s) and whether to deploy Additive, Subtractive, or both to achieve optimal part/assembly design and performance.
We seem to be on this technology Sine curve where new technology arises that is way too expensive for most. Then technology advances in software and hardware making the new technology affordable to most all. Then the next great technology arises, again way too expensive for most to afford. New advances make it more achievable and then, someone has an idea to integrate the older technology to the newer to produce amazing new hybrid tools, utilizing the very best of both worlds. I was fortunate enough to have experienced living through many of these technology spurts and cannot wait to see what is available to greet me on my 100th birthday!
Joel Pollet, Cimquest, Inc.
Leave A Comment