The push for electric vehicles (EVs) is nothing new, but few expected the arms race Tesla would spark in the automotive world with their aggressive development. Now, IHS Markit predicts that 25 percent of all passenger vehicles sold worldwide will be electric by 2030. Others predict that even more will be sold by then. Currently, the inventory of automobiles, in general, is less than demand because of the supply chain issues of 2020 and 2021, leaving the market wide open for accelerated growth.
The automotive manufacturers that learned from the pandemic reassessed their production processes to maximize cost containment. Often that meant optimizing their CNC machining approach. Luckily, that exact choice will make it easy to switch from manufacturing mainly internal combustion engine (ICE) vehicles to EVs. That switch will be more difficult for shops that have overly specialized equipment, but investing in the right software in the coming years could put them back on the right path.
The most obvious concerns when producing EVs rather than ICE vehicles are reducing weight, achieving the precision necessary for making battery packs, and producing internal components with longer lifespans than their ICE counterparts. The right software and machining centers will help manufacturers move quickly from prototyping to mass production, in time to meet regulatory deadlines and even just to stay competitive.
Reducing Weight
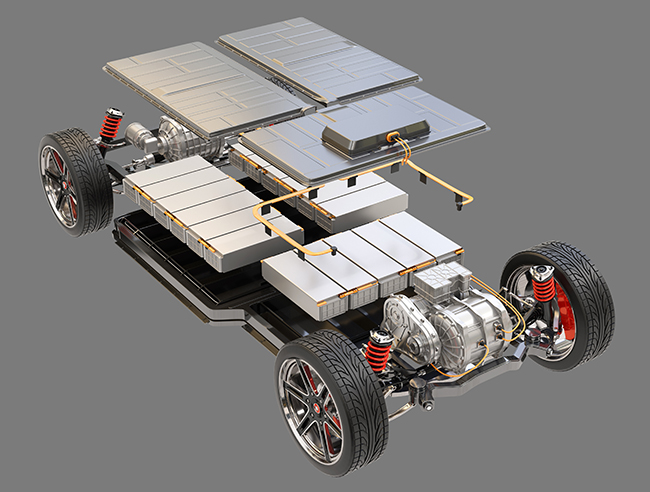
Explode view of electric vehicle chassis equipped with battery pack on gray background. 3D rendering image.
Any part of a modern EV has been designed, modified, and redesigned to eliminate weight, drag, and friction as much as possible.
- Body panels are made from innovative dies, which are machined by powerful 5-axis machining centers.
- Internal components are pocketed to reduce overall mass. Reaching these compartments without multiple setups would be impossible without multiaxis machining.
- Lightweight aerospace materials are used for many of an EV’s parts, but often these are difficult to machine with traditional processes. Without CAM software that offers detailed simulations and continuously monitors the machining process, the risk of gouging or warping is high.
Machining Batteries
The battery pack of an EV is essentially a Russian nesting doll of components: battery cells within battery modules within the battery pack attached to the vehicle frame.
Parts like rotary shafts, linear ball bushings, and configurable plates can only be made with extremely precise machining.
Batteries need to be protected from vibration and environmental factors (extreme temperatures, moisture, etc.). Their seals must perform even better than those in an ICE, because electric motors operate at greater speeds and temperatures.
Meeting Tight Tolerances
Even though they perform at high speeds and temperatures, consumers expect less maintenance on EVS. There are fewer overall components in an electric motor, so each must be flawlessly manufactured for OEMs to meet this expectation.
Parts must have perfect surface finishes that require little deburring.
Any pocketing that is done must not alter the strength of the machined part, so each stepover and stepdown must be accurate to thousandths of an inch.
The Right Tools
Automotive manufacturers should seriously consider reorganizing their shops and processes to make way for EVs. The best way to do that is to invest in the right equipment, and the right CAD/CAM software for the job is Mastercam.
- Mastercam Multiaxis automatically generates optimized toolpaths for making automotive dies and for producing complex parts with deep pockets.
- Dynamic Motion Technology monitors the stock material during the entire cutting process, automatically adjusting feeds, speeds, and tool angle to keep machining safe and efficient.
- Verify and Backplot functions accurately simulate every stage of machining and highlight possible mistakes, gouges, and collisions.
- Extremely accurate toolpaths can meet even the tightest tolerances.
Click below for more information on Mastercam CAD/CAM products.
Leave A Comment