MAG Orthotics, based in Sheffield, UK, is at the forefront of revolutionizing the orthotic and podiatry industry through the adoption of advanced 3D printing technology. By partnering with Additive-X and Fit360, the company is moving away from traditional manufacturing methods, aiming to enhance efficiency, sustainability, and product quality through a fully digital workflow.
Challenges in Traditional Orthotics Manufacturing
The orthotic industry has long relied on conventional manufacturing processes, which are often labor-intensive and time-consuming. Traditional methods typically involve manual casting and molding, which not only require significant time and labor but also produce substantial material waste. This approach has made it difficult for companies to scale their operations efficiently and sustainably.
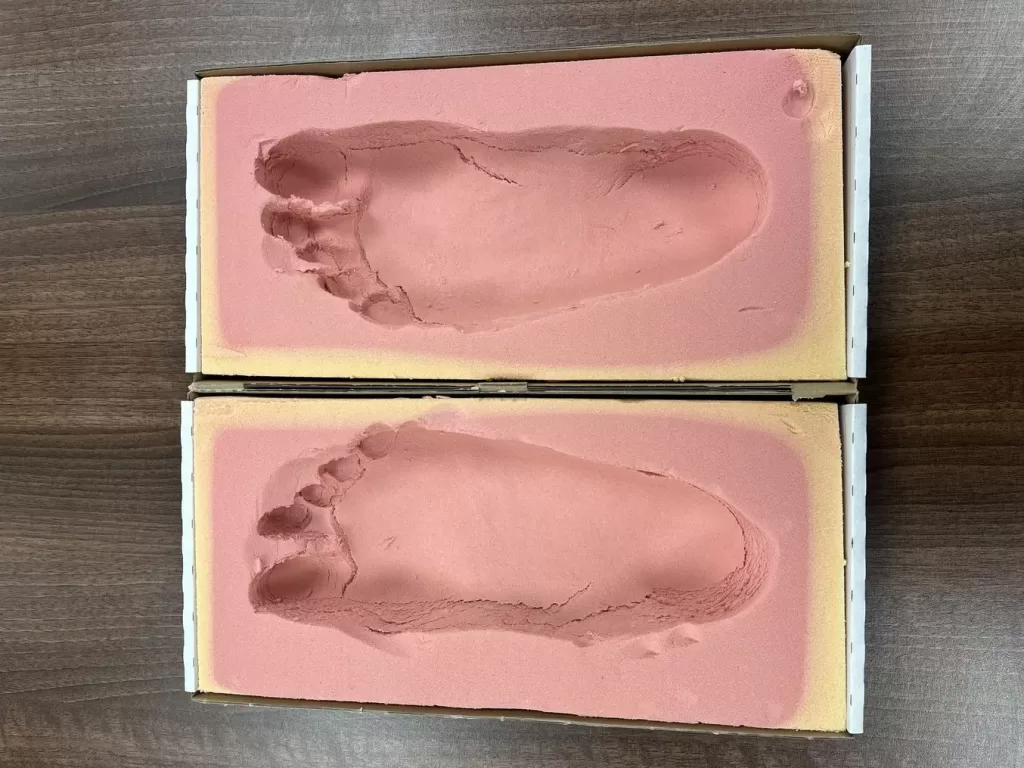
Some orthotists and podiatrists still send a physical foam impression box (FIB) to MAG Orthotics.
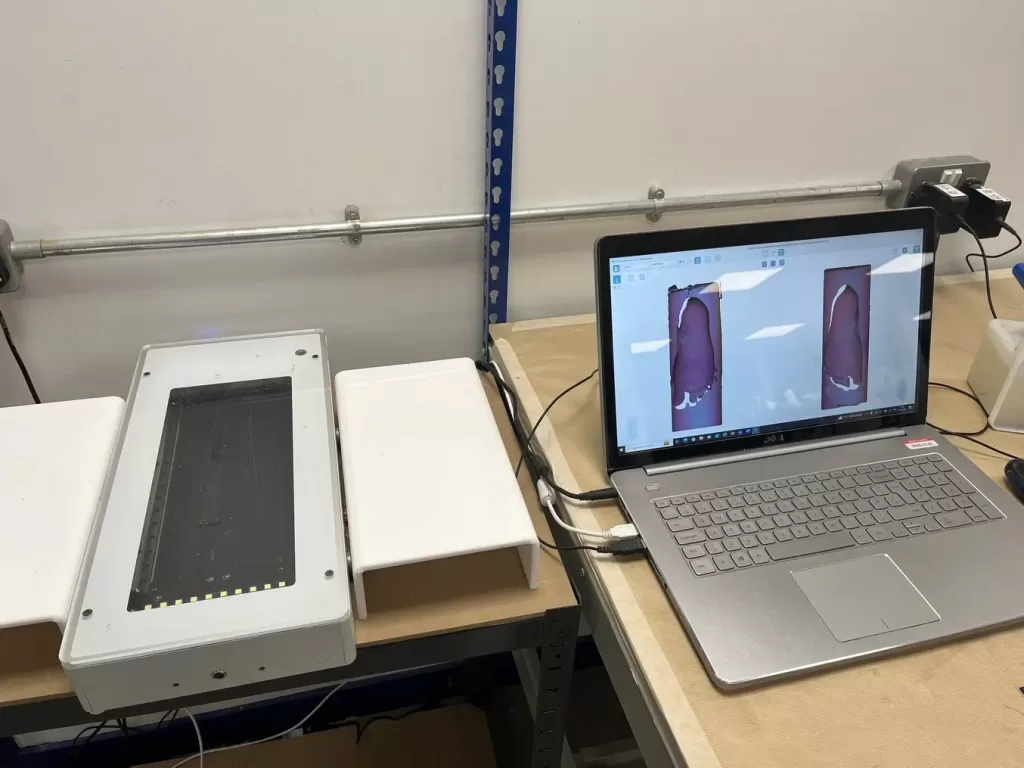
FIBs must first be scanned, adding time over a purely digital workflow.
Moreover, the bespoke nature of orthotic products means that each insole must be custom-made to fit the unique contours of a patient’s foot. This customization adds another layer of complexity and potential for error in the traditional manufacturing process.
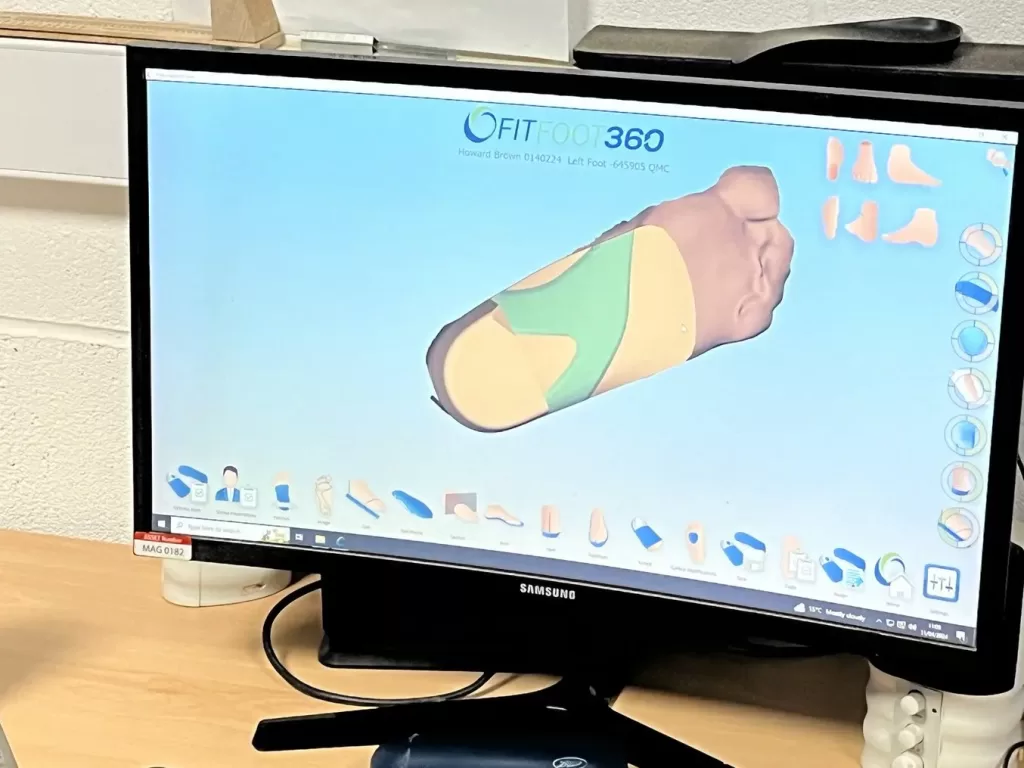
MAG Orthotics uses Fit360 software to design their insoles.
Embracing 3D Printing for Efficiency and Precision
Recognizing the limitations of traditional methods, MAG Orthotics has embraced 3D printing technology to streamline production and improve the quality of their products. The integration of Formlabs‘ Fuse 1+ 30W printers into their production line has been a game-changer. These advanced printers enable the rapid and precise manufacturing of custom insoles, significantly reducing the time from design to delivery.
3D printing allows for the exact amount of material needed to be used, minimizing waste and aligning with the UK’s stringent zero-waste policies. This shift not only contributes to environmental sustainability but also reduces material costs and enhances overall production efficiency.
The Role of Partnerships in Driving Innovation
The transformation at MAG Orthotics has been significantly supported by strategic partnerships with Additive-X and Fit360. Additive-X, a leading provider of 3D printing solutions, has been instrumental in providing the technical expertise and support necessary to implement this new technology. Their guidance has helped MAG Orthotics navigate the challenges of transitioning from traditional to digital workflows.
Fit360 has contributed by providing state-of-the-art scanning technology that ensures precise measurements for custom insoles. This technology captures the exact contours and dimensions of a patient’s foot, allowing for the creation of highly accurate and comfortable insoles. The combination of precise scanning and 3D printing has resulted in a product that is not only tailored to the individual needs of each patient but also produced more quickly and efficiently.
Benefits of a Digital Workflow
The move to a digital workflow has brought numerous benefits to MAG Orthotics. One of the most significant advantages is the reduction in production time. Traditional methods can take several weeks to produce a custom insole, whereas 3D printing can accomplish the same task in a matter of days. This rapid turnaround time means that patients receive their custom insoles much faster, improving their overall experience and satisfaction.
Additionally, the digital workflow enhances the consistency and quality of the products. 3D printing technology ensures that each insole is produced to the exact specifications, reducing the likelihood of errors and variations that can occur with manual methods. This precision leads to better-fitting insoles, which can significantly improve patient outcomes.
“On an EVA from a CNC, you’ve got all your flash, the wastage you have to cut off, and you have to put the templates on, cut round all that, then smooth it all in, shape it all, so it takes a lot longer. This is why we like 3D printed insoles, because they’re a lot quicker and a lot less work on the bench.”
Lee Lingard, CAD and 3D Development Specialist, MAG Orthotics
Commitment to Sustainability
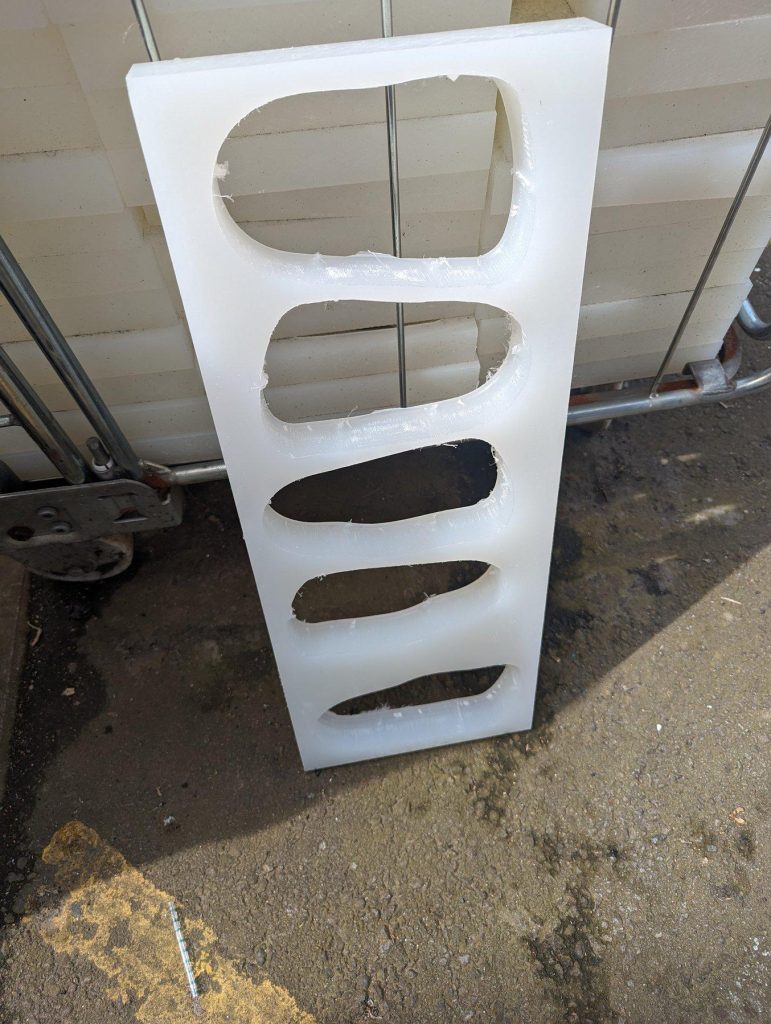
Polypropylene material waste from CNC manufacturing adds up quickly.
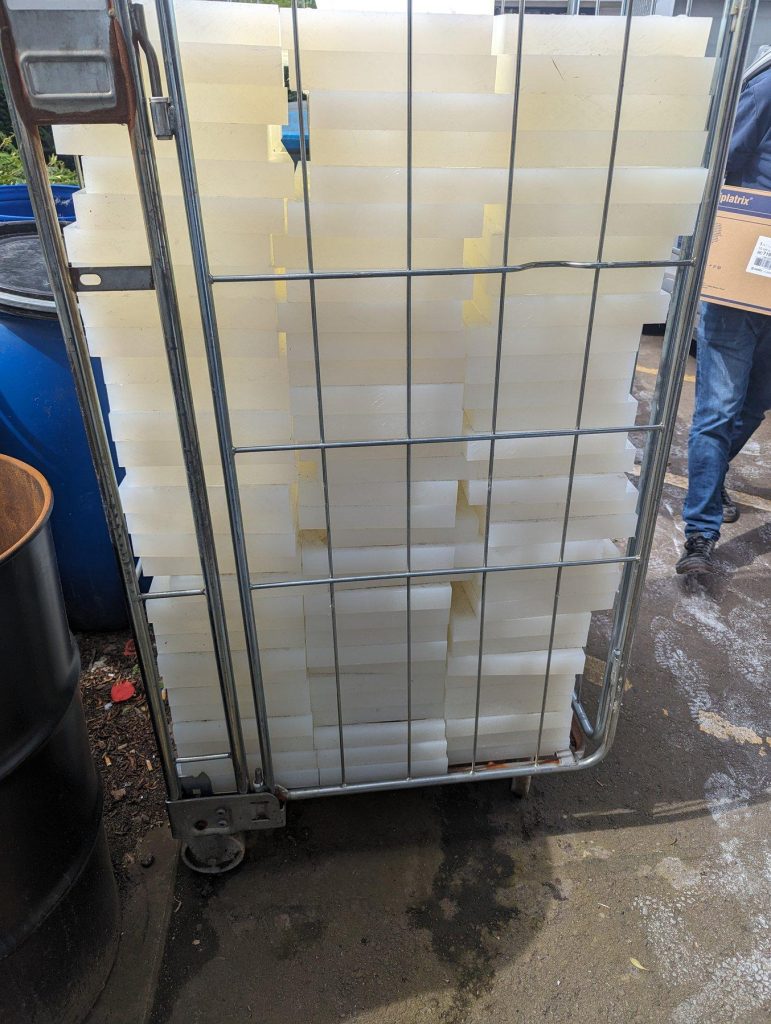
Reducing this accumulated waste is a primary reason MAG Orthotics has adopted 3D printing.
MAG Orthotics’ adoption of 3D printing technology is also a testament to their commitment to sustainability. By reducing material waste and embracing more efficient production methods, the company is taking significant steps toward minimizing their environmental impact. This commitment aligns with broader industry trends and regulatory requirements aimed at promoting sustainable practices.
“We used to use a lot of plaster, so it’d be hand-molded with plaster and then molded around the plaster with EVA or polypropylene. We then moved forward and we started using CAD design and using CNC machines to mill them, but there was still a lot of waste. But with powder and TPU there’s very, very little waste and that’s the way forward environmentally.”
Mark Joyce, General Manager, MAG Orthotics
Setting a New Standard
Through their innovative use of 3D printing technology, MAG Orthotics is setting a new standard in the orthotic and podiatry industry. Their ability to produce high-quality, custom insoles quickly and sustainably is a clear demonstration of the potential of digital workflows. As more companies in the industry begin to recognize the benefits of 3D printing, it is likely that MAG Orthotics will serve as a model for future innovation and development.
Contact us to learn about 3D printing orthotic insoles or to talk to a 3D printing expert to find the solution that’s right for your business.
Leave A Comment