
However, our primary goal is in using the printers to educate. And that leads me to my topic today…
uPrint / Dimension vs Fortus
This entry concerns the FDM (Fused Deposition Modeling) line of printers by Stratasys. Digging a little deeper I will be comparing some, but by no means all, aspects between the
Dimension / uPrint printers…
And the Fortus printers…
The uPrint and Dimension lines are, mechanically, almost identical. The major differences within the uPrint and Dimension lines are support material, layer resolution, build envelope and ability to print in color. But as far as the hardware and ability to create models, they all have roughly the same performance.
The Fortus line, however, is in a league of its own. For many reasons (hardware accuracy, stability, material choices, layer resolution, reliability, repeatability) it is a much higher performance machine. As such it makes sense you would want a way to take advantage of that performance.
Enter… Insight. Insight is the software used on the Fortus line of printers which prepares a 3d file for printing. The uPrint and Dimension lines, in contrast, use software called Cadalyst.
So what?! You ask with rapt attention. Well this is where I have used our printers for the greater good. I prepared a comparison model to illustrate the differences between Dimension / uPrint (Cadalyst software) and Fortus (Insight software).
The model on the left was printed on the Fortus and the model on the right was printed on a Dimension Elite. To be fair the model on the left was printed in Polycarbonate whereas the model on the right is ABS. This illustrates the benefit of being able to choose your material.
At first the dissimilarities probably do not seem drastic. But when you start to look closely you see a few issues…
The most obvious difference is layer thickness. The Fortus model (left) was printed at .005” while the Dimension model was printed at .010”. Some Dimension printers can print at .007” but all of the uPrint and Dimension printers can print at .010”, so I chose that resolution for our comparison.
The yellow arrow points at a specific artifact on the ABS model. You can see at this stage in the print the overall build seems to have shifted a bit. This caused an offset in the door feature on the model. The green arrow shows a little bit of bulge in the material.
Between the outside building wall and the inner wall of the window frames the ABS / uPrint / Dimension model (now on the left) shows what could best be described as “ghosting.” This is the result of the same issue that caused the offset in the door on the image we saw last. Here is what is happening. When these printers lay down a bead of material the print head is being zoomed across a gantry. You would think the faster it can do this, the faster it can print. However the flip side of speed is stopping. A printer follows a cnc path dictated by a sliced 3d model (the output of either Cadalyst or Insight).

Say you are in a race car and you have a sharp right angle coming up. You happen to be driving a BMW M3. Not too shabby. You zoom through that curve and cut it as tight as you can. Here is what your path looks like on the track…


You were able to cut that turn close and stay in control even despite a higher speed. I am sure you see where I am going with this. The road way is the path as defined by the 3d model. The path of the car is the bead of material being laid down. Due to the higher performance the Formula One Car (the Fortus) is able to hit those turns better, faster and more consistently. Performance on the Fortus is due to a larger supporting frame size (allowing more power and control) and more accurate gantry systems (ball screw versus belts).
So what is happening with the ghosting is the print head is over steering or under steering the path because it is being required to make quick XY adjustments. Each of these paths is laid over the last and so tiny variations (over steering or under steering) in laying the bead path can show on your model as a slightly offset or ghosted feature.
Let’s look at another picture…
You can see that the model on the left has some air gaps between the walls. Why? Well the wall in this case is .024” thick. We are printing at a resolution of .010”. So naturally you will lay down the outside walls first. That leaves .004” of interior. The Dimension simply cannot fill that area.
So how does the Fortus handle this? Well, using the Insight software you can control your bead thickness and maintain your z layer resolution. So you can tell the machine to lay two paths of .012” which fills this feature out perfectly. Thanks to this capability you almost never need to have hollow walls.

Another example is on the back porch wall of the Brownstone…

To be clear you do get accurate, repeatable results with both technologies, in addition to strong, functional, stable prints. The purpose of this was to illustrate how much more you get with the Fortus line and to illustrate the reason behind the difference in cost. To summarize with Fortus you get:
• Faster print speeds / higher throughput
• Increased repeatability / accuracy between prints
• The ability to control build paths to optimize your models as per your requirements
• Additional material options
• Better accuracy as compared with the 3d model / cad data.
There are plenty of other factors I did not touch on here such as z layer adhesion and support modeling options. Those will be covered in subsequent posts. But hopefully this served as a useful illustration on some of the advantages in the Fortus system.
If you have more questions or need more information on 3D Printing solutions or how you can get your parts printed with Cimquest 3D Print services, contact us here and we’ll get back to you ASAP.
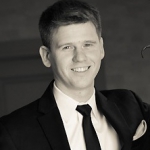
Jim Snodgrass graduated from Arizona State University in 2008 and assists in everything from Marketing to Prototyping to Business Development at Cimquest. He enjoys spending time with his wife and Son and occasionally making meager progress renovating his house.
Leave A Comment