XYZ Printing’s SLS machines can be used to reduce waste and provide more cost efficiency, making additive manufacturing greener. (Sponsored Content)
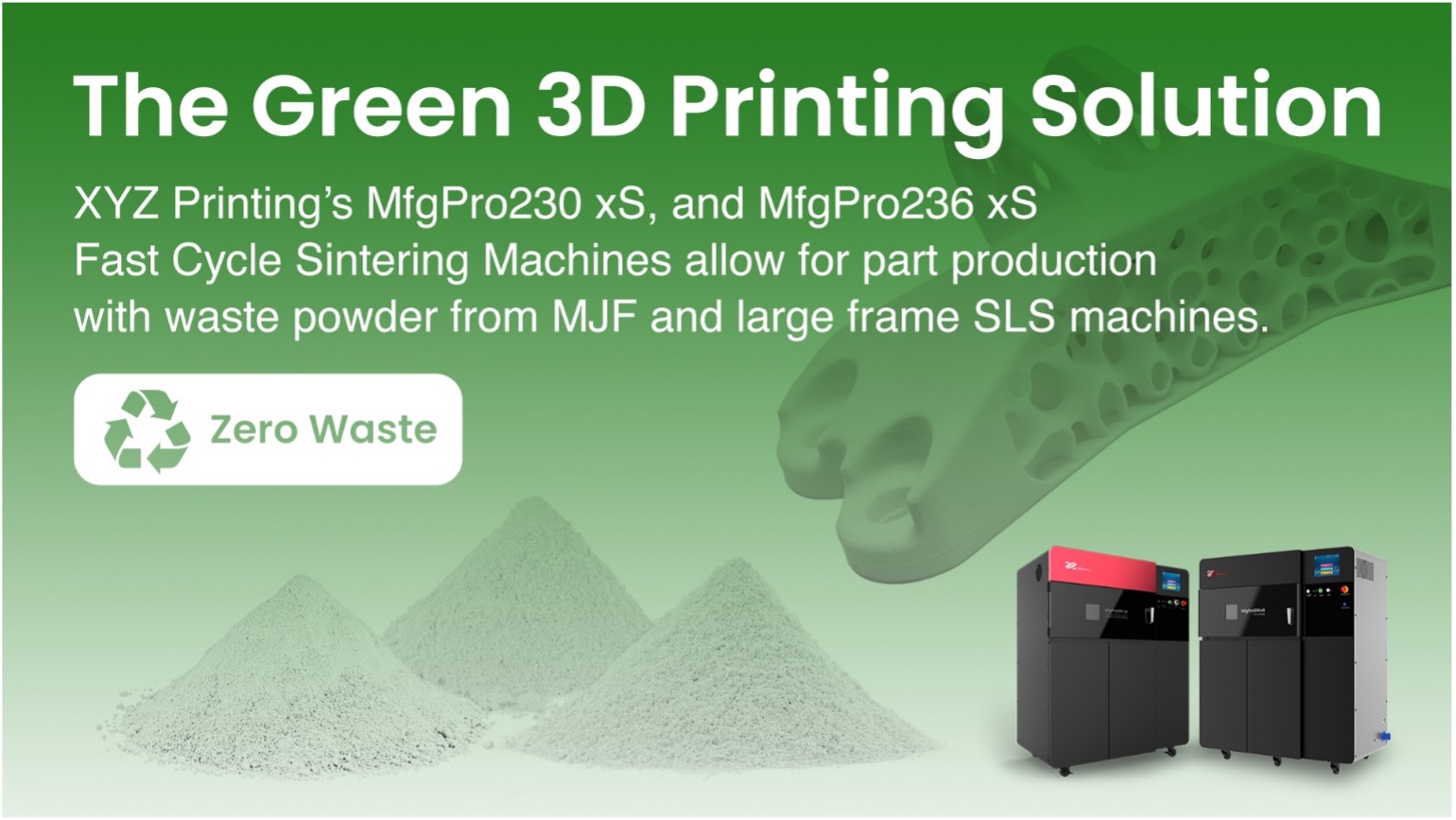
Fully Recycled PA12 Part from mixed MJF and SLS waste, XYZ MfgPro236, MfgPro230
All forms of 3D printing provide incredible value in terms of innovation, speed, communication, and customization. This novel technology’s advantages have outweighed the downsides, such as cost, electrical usage, and hazardous and non-hazardous waste.
SLS technology reduces waste by using essentially reusable thermoplastic powders. However, depending on the platform you select, the critical factor of recycling material remains.
Some SLS machines have material recycling efficiencies as high as 80/20 (meaning the refresh rate is only 20% for un-sintered powder). Others require fresh powder at a rate of 50%, and these tend to be large-format machines that print larger parts. Hazardous or not, it presents a significant issue of end-of-life powder waste for machine owners, especially those working with multiple machines.
Service bureaus and businesses with more than five large-format SLS and or MJF machines face a storage dilemma as the wasted powder stacks up. How much do they have to pay for disposal, and what is the environmental impact?
Despite the advantages SLS 3D printing provides over other manufacturing technologies, many of these machines can be wasteful. In the case of MJF 3D printing, polyamide and other SLS powders essentially liquify and flow from the energy of the laser or thermal system.
While the powder not being sintered or fused isn’t melting or flowing, it is still subjected to damaging heat. Longer heat cycles for larger builds cause more damage and waste. Typically, these voluminous builds require a higher ratio of fresh powder. As a result, waste is higher with large-format SLS machines. Conversely, a smaller build volume SLS machine prints and cools down much quicker (as much as 10X faster). This speed benefit is twofold, parts are available every 24 hours, and the waste factor is significantly reduced, so overall print costs are lower.
This is a significant and counterintuitive fact of using large-format SLS or MJF machines for serial part production. Many would naturally assume a big machine with a large build volume is most efficient for production. In reality, a small build volume SLS is typically faster, provides exponentially faster cooling, and is more efficient in reducing waste.
If improving efficiency and reducing waste isn’t advantageous enough, the other primary benefit of small SLS machines, such as the XYZ MfgPro 230, is the overall cost. The platform’s price in the case of the XYZ MfgPro 230 is about 1/5th that of large format SLS or MJF 3D printers. Machine redundancy and material choice flexibility are other significant advantages of going small and adopting multiple small SLS machines.
In addition to larger machines having a higher waste factor, most also have a locked material system. This means the user can’t change parameters enabling them to buy material from a company other than the machine manufacturer.
In most cases, few of these manufacturers make their powder, and all buy from the same patent-protected powder manufacturing companies. The more they sell, the more buying power they have with the powder supplier. This starts a vicious cycle that leads to more powder waste than ends up in landfills.
XYZ Printing has a different approach, leveraging high-performance smaller build volume SLS machines that print with high part quality while producing less waste – all within an affordable open platform system. An open platform system allows users to decide which powder they want to utilize and purchase from any material supplier.
Another key benefit of this open platform system is that it allows the user to fine-tune the heat variables in SLS printing. These parameters can be preset to allow powder deemed waste by other SLS and MJF systems to be used in the XYZ SLS platform, while still producing high part quality and accuracy ¬– with no significant difference in mechanical properties.
Consider a large 3D printing service bureau with an array of large SLS machines running concurrently. In this realistic scenario, the service provider would likely have drums of waste powder separated from each machine, waiting to be disposed of. Again, the cost of disposal and overall wastefulness is not trivial.
These powders have been damaged during the heating cycle and no longer produce viable parts. The user is unable to make parameter changes and utilize the leftover material. For many SLS machines, the powder is even more damaged than that of the MJF machines due to longer cycle processes. MJF machines have an optical sensor that reads the color of the powder and rejects it when it becomes slightly discolored. While it will no longer work for MJF due to a slight coloration, the health of the powder is actually very good for use in an open platform XYZprinting SLS machine. Hence the adoption of XYZ machines in world-class service bureaus like JawsTec.
As illustrated here, end-of-life or waste powder on a large-format SLS machine can be mixed with 20-30% fresh XYZ powder and get great results. One innovative solution for these multi-platform users is to mix the HP MJF PA-12 end-of-life powder with the end-of-life PA-12 powder from an EOS or 3D Systems machine.
XYZ machines can use this combination of PA-12 “waste product” to produce high-quality low-cost parts while solving a big problem that has hindered the adoption of additive manufacturing. To learn more about XYZprinting SLS 3D printers, register for their upcoming webinar on Thu, Sep 29, 2022 11:00 AM – 12:30 PM EDT.
Leave A Comment