The Audi Sport Quattro road and rally car has captivated many automotive enthusiasts since its first launch around 40 years ago. Some even call it the “legend of motorsports”. That’s why two companies passionate about motorsports decided to recreate it with the help of 3D scanning and 3D printing.
On one hand, LCE Performance led the way with its long-standing experience in automotive tuning and engine technology. On the other, Downforce Racing brought its carbon-brazed part development services to the table.
The teams collaborated to reproduce the Audi Sport Quattro with carbon parts and CFD simulations. Their replica looks stunning:
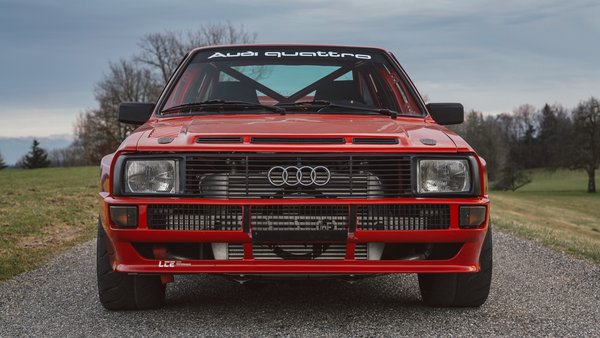
A replicate of Audi Sport Quattro by LCE Performance
The main challenge of improving the performance of the racing car
In this project, the main challenge was dealing with legacy parts. Many of the race car’s original parts are no longer in production as a result of its lengthy history.
Even if second-hand parts were available, they were expensive to buy and difficult to renovate. “They’re 40 years old and look shabby. I pretty much can’t refurbish them at all.” Steven from LCE Performance said.
For a company wanting to focus on providing high-quality, durable parts for its customers, these poor second-hand parts were not an option.
3D scanning with FreeScan UE Pro for reproducing parts
There are two ways to address these challenges using 3D scanning technology. The first is to replicate a new part by scanning the original, while the second is to scan a race car and develop a design from scratch.
In this case, LCE Performance 3D scanned the car’s entire frame. The team used the SHINING 3D FreeScan UE Pro with the help of the 3D Scanning Academy. They removed the fenders and add-ons before 3D scanning the chassis, to get a clean 3D model more easily.

Scanning the chassis using SHINING 3D FreeScan UE Pro
Then they scanned the vehicle body completely. This was to determine whether the vehicle’s main geometries were intact, or if they had been damaged in a potential accident.
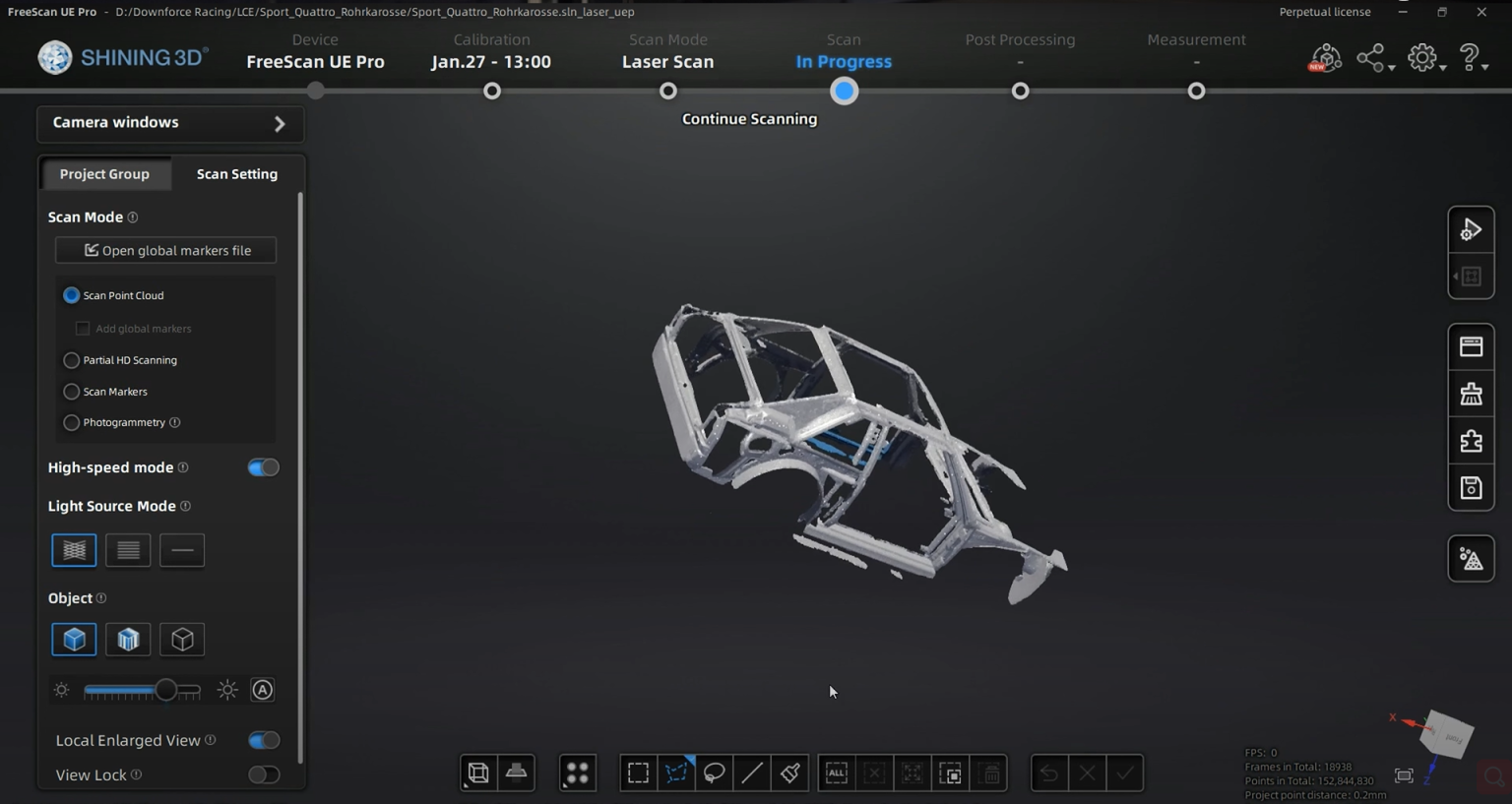
Partial 3D data of the car body
Using the FreeScan UE Pro’s Rapid Scan mode, the team was able to easily and quickly acquire high-quality data, even on such a large object. Plus, they didn’t need to spray the dark, carbon parts.
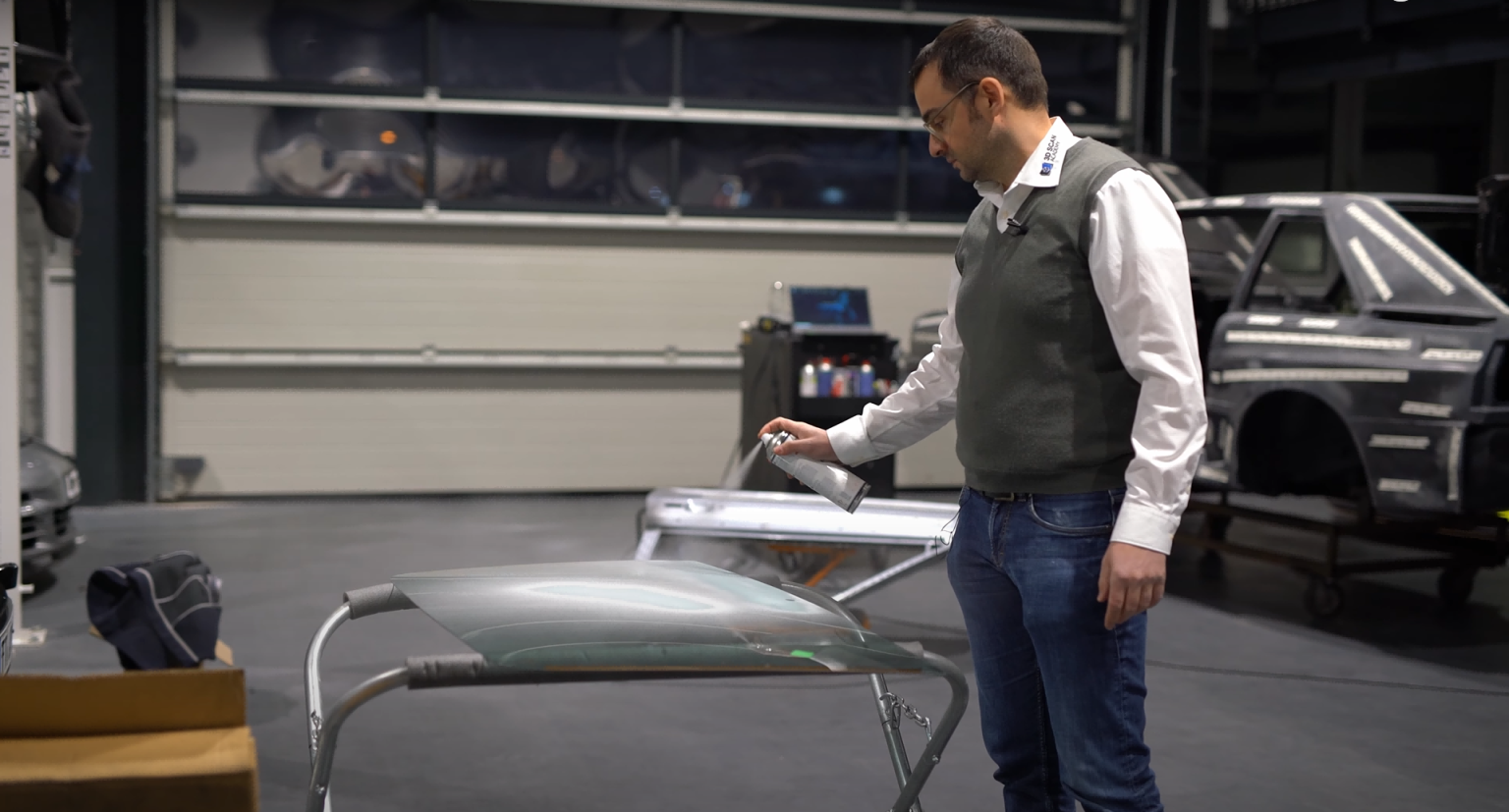
Spray transparent car windows for easier 3D scanning
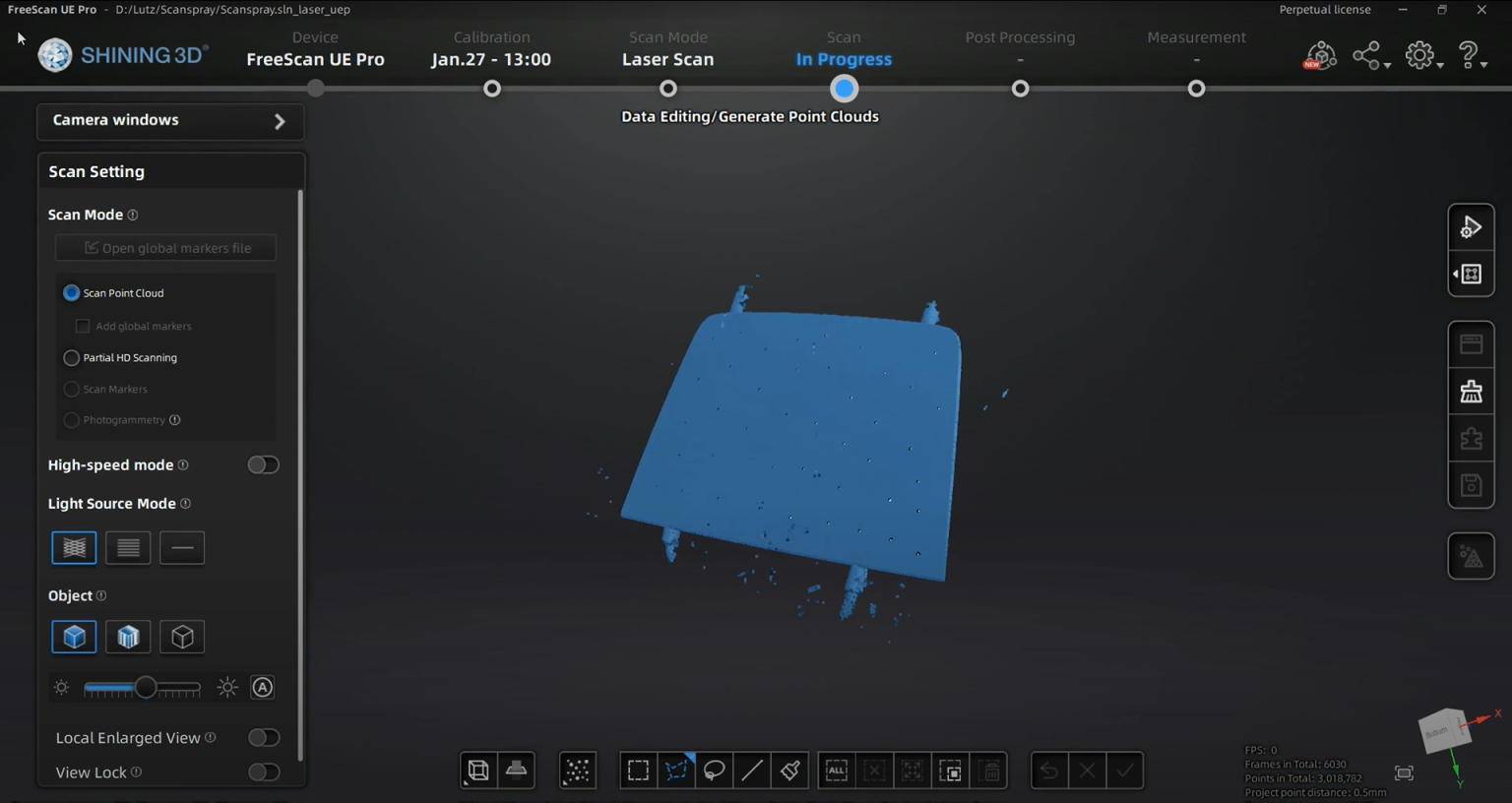
3D data of the car window
3D scanning and 3D modeling for CFD simulations
After the 3D scanning session, it was time for Downforce Racing to step in. They used LCE Performance’s clean, accurate 3D data to create standalone 3D models.
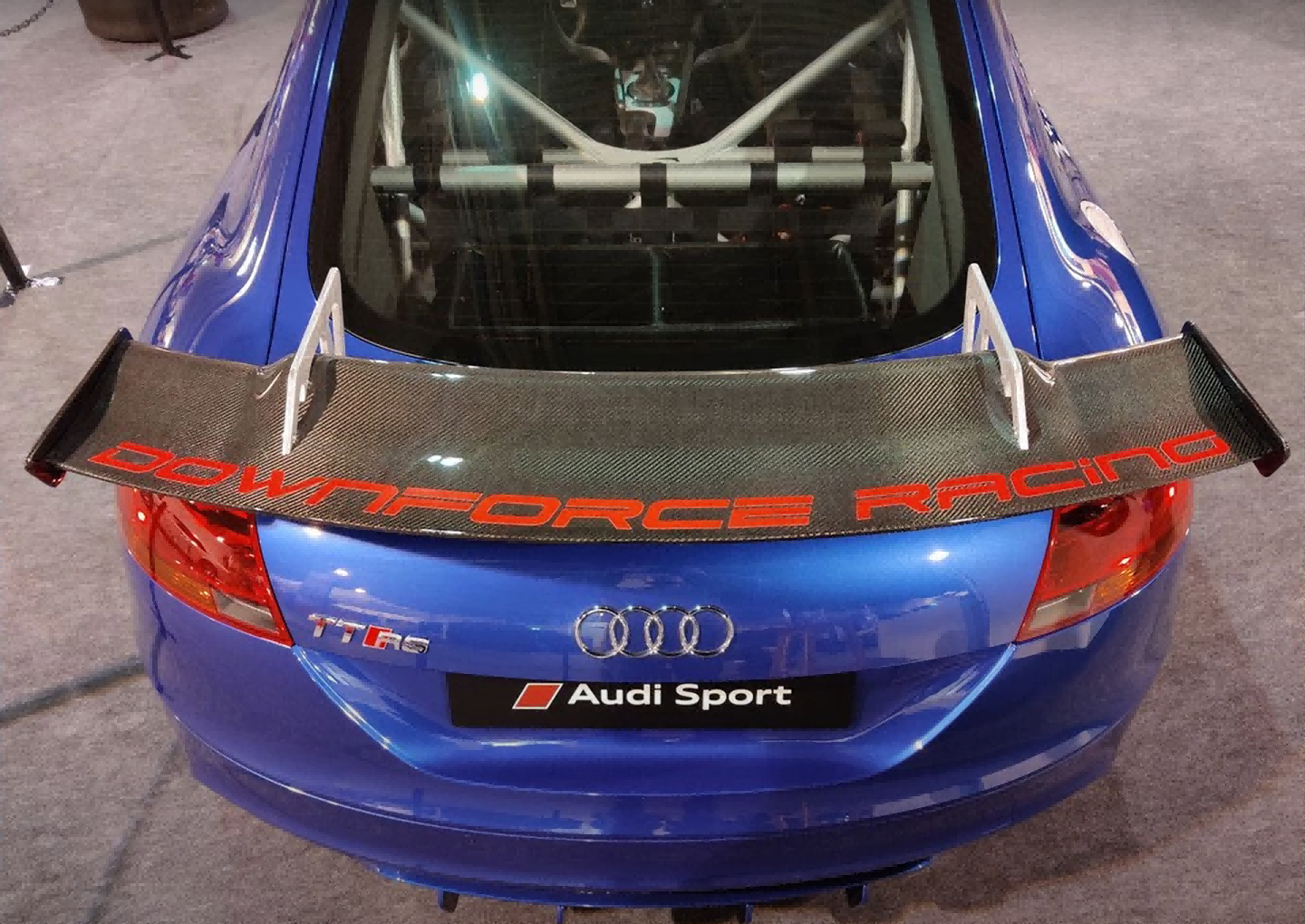
A carbon part made by Downforce Racing
Additionally, 3D models generated by 3D scanners and some reverse engineering were used in CFD simulations to improve car performance. CFD is a simulation tool used to analyze and predict the behavior of fluids and gases in motion. By using CFD simulations, the team was able to test and optimize the design of the new carbon parts before they were manufactured. This allowed them to improve the aerodynamics of the car and reduce drag, resulting in better performance on each drive.
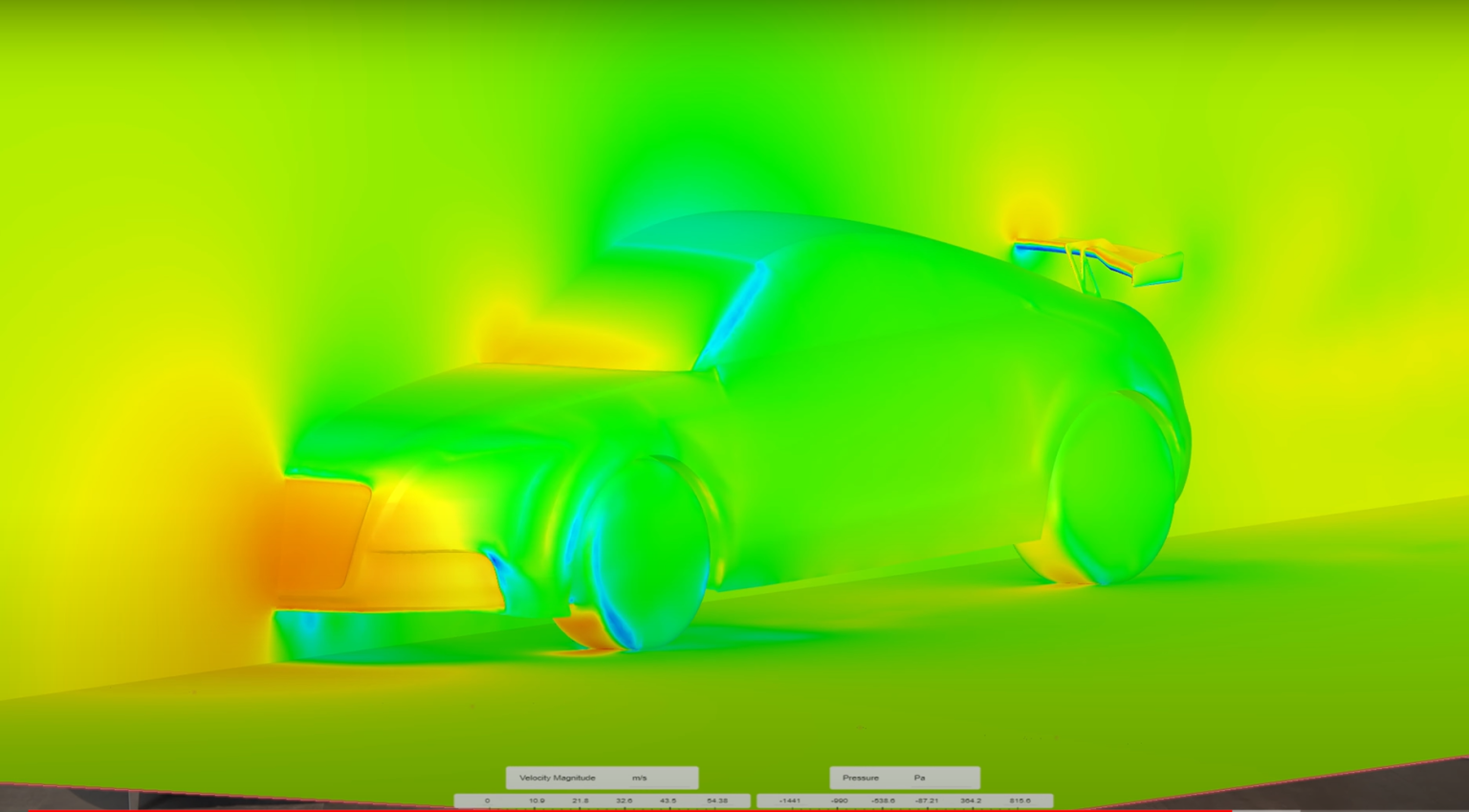
Run CFD simulations to test the racing car’s performance
The success of the partnership between LCE Performance and Downforce Racing is due in part to their effective use of 3D scanning technology. This showcases the invaluable role that 3D scanning plays in the field of racing cars, particularly in overcoming the challenge of reproducing parts with precision and improving racing car performance.
Leave A Comment