Why is 3D scanning often preferred for reverse engineering, and how does it compare to contact probing methods?
There are pros for non-contact scanning and there are pros for tactile probing methods, but for many parts scanning works better or is essential. Following is a look at the benefits of 3D scan to CAD, and what might be better suited to probing. A hybrid of both techniques may be the best approach at times.
Pros for scanning:
- 3D scanning makes it easy to obtain 100 percent coverage including fine detail, critical for formed sheet metal panels.
- While simple geometric features like planes, holes, and flats can be measured with hand tools such as calipers, micrometers, and height gages, shapes that are non-geometric, complex contours (for example, an aircraft airfoil or an automotive body panel) cannot easily be reverse-engineered with gages.
- Soft, non-rigid parts are not suitable for contact probing since they deflect when touched by contact probes or gages. Also, some are delicate, and therefore, it is desirable to use non-contact methods. Super-complex, organic shapes (such as a person or animal intended to be manufactured as a figurine) are almost impossible to reverse engineer using contact probes or gages.
- Scanning gathers a lot of data quickly, so it can be a major productivity tool. While contact probing with CMM-type devices is often used for reverse engineering, non-contact scanning can make it faster and easier.
- 3D scans can cover the entire part, including fillet radii and fine details that are desirable to be captured.
- There is no need for probe compensation. Contact probes use a ball-type tip or “stylus,” the center point that must be captured and offset to the theoretical contact point by the measuring device and 3D scanning software.
Pros for probing: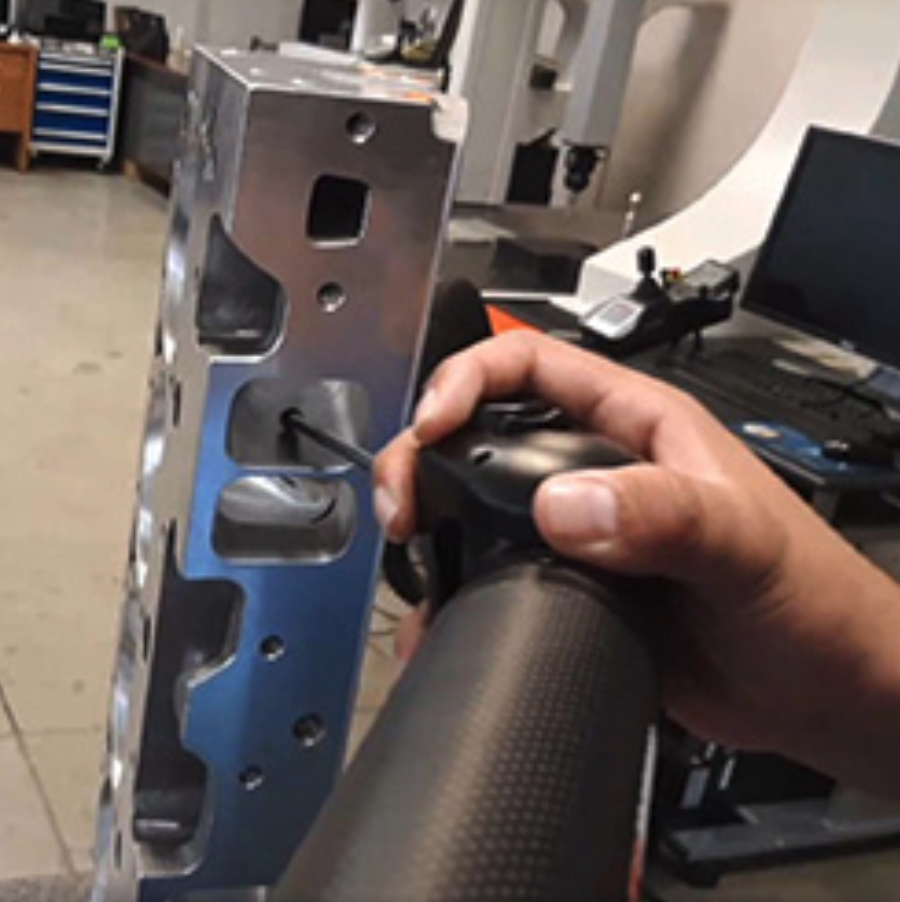
- For non-line-of-sight inner features beyond the reach of non-contact scanners, tactile scanning with a contact probe works well.
- Probing and gages can be more accurate than scanning. Most scanning methods are said to contain around 0.002 in. (0.05 mm) accuracy error on average. Contact probing and gages can produce more accurate results.
- Non-contact scanning is line-of-sight measuring and often cannot obtain good data inside holes or obscured features. Most of the time these types of features can be digitized with contact probes.
- Scanning provides a lot of point cloud or mesh data. Large data files can be burdensome to handle, often challenging for computer performance and storage. The large datasets can include an overabundance of data that is more intrusive than beneficial. It usually takes time to clean the data of erroneous “overspray” or “noise.” It can take longer to turn a dense point cloud into a feature or surface than probing or hand-gaging it.
- Scanning systems typically are a much larger investment than probing.
- Scanning can have many of issues with surface reflectivity, color, or finish. It may take a while to get a good scan, or may not be possible at all. Often times parts must be sprayed with some type of coating to allow scanning.
Contact us to learn more about reverse engineering.
Leave A Comment