Traditional molds for silicone part production are CNC machined from blocks of aluminum or steel. These include two-part or multi-part injection molds for liquid silicone rubbers (LSR), or single cavity compression molds used with a heat-cured rubber (HCR) silicone sheet that is cured under pressure and high temperature. Normally these types of metal molds are used in mass production. However, when employed for prototyping, lead times of several weeks and upfront tooling costs of hundreds to thousands of dollars limit a designer’s ability to implement and test small changes in a mold design.
Desktop 3D printing is a powerful solution to fabricate tools rapidly and at a low cost. It requires very limited equipment and enables skilled operators to focus attention on other high-value tasks. With in-house 3D printing, manufacturers and product designers can introduce rapid tooling into the product development process to validate design and material choices prior to transitioning to mass production. They can iterate quickly, accelerate product development, and bring better products to market. 3D printed tooling using Formlabs SLA resins offers many advantages to product designers across prototyping, small-scale production runs, and custom part production. Using 3D printed tooling, RTV two-part silicones are injected into a two-part or multi-part mold or an RTV silicone putty is squeezed between sections of a 3D printed compression mold. Using 3D printed tooling, a broad range of tin cure and platinum cure silicones are available to designers, including a wide range of durometer ratings, colors and degrees of transparency, as well as special functions such as skin safety.
Stereolithography (SLA) 3D printing technology is a great choice for silicone mold tooling. SLA parts are characterized by a smooth surface finish and high precision. RTV silicone rubbers capture fine surface details including defects, so the quality of the tool surface directly translates to the surface quality of the final part. A mold printed with a fused deposition modeling (FDM) printer, for example, would leave visible impressions of printer layer lines in the silicone part.
By contrast, SLA 3D printing with Formlabs BioMed Clear Resin or Clear Resin allows for visualization of the silicone injection process, enabling designers to assess bubble and void formation, and identify areas where corner fillets or additional air vents should be added. SLA 3D printing also offers an advantage for design complexity; a 3D printed mold allows designers to take advantage of undercuts or other complex geometries that may not be possible or would be prohibitively expensive to produce with CNC machining.
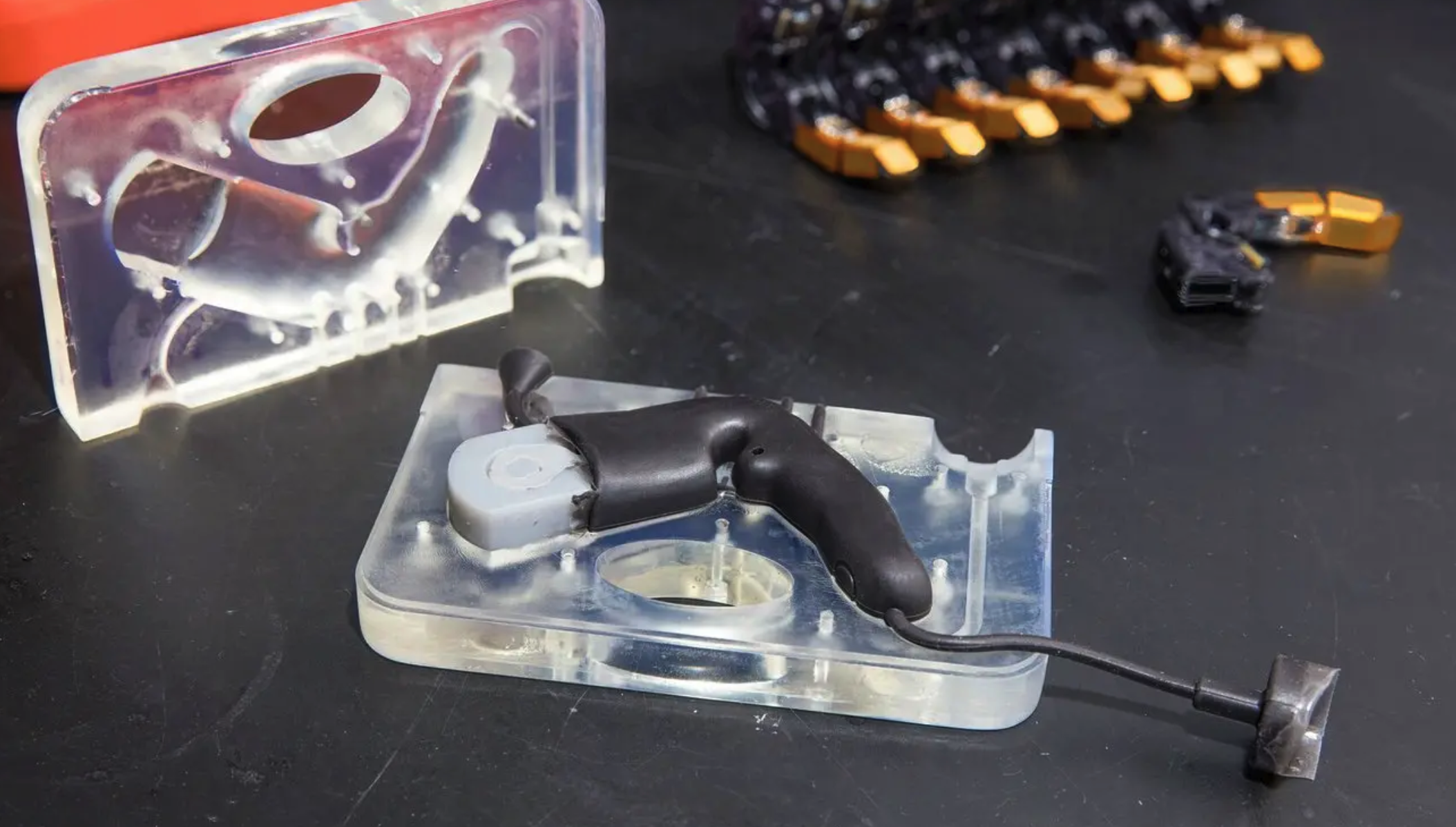
PSYONIC encapsulates the Ability Hand fingers using a silicone overmold configuration. Some molds include a Tough 2000 Resin mold insert to anchor the encapsulated “bone” feature in the mold.
Formlabs BioMed Clear Resin and Clear Resin are also quite versatile in their mechanical performance. The same material can be used for an extremely thin eggshell mold that cracks away easily from a custom silicone part, or for a robust compression mold that is used multiple times to produce gaskets. Finally, using affordable benchtop scale fabrication reduces lead times; a designer can print a mold geometry and start injecting silicone the next day.
When used with 3D-printed molds, RTV silicone rubber captures fine surface details, including embossed text. In addition, most castable silicones are not chemically adhesive and will peel away from the mold surface after curing. Mechanical bonding can be achieved by casting onto highly porous surfaces like woven fabric. In some cases, chemical bonding can be promoted with specialized binders.
Because processing RTV silicone does not require high heat or pressure, it can easily be formed with limited equipment in a prototyping lab, reducing the startup cost needed to introduce soft parts to any company’s design portfolio.
For more information on Formlabs materials, please click below.
Leave A Comment