Advancing Orthotics & Prosthetics through Digital Innovation with Freeform
Luca Gualerzi, a Certified Prosthetist and Orthotist (CPO), leads Ortopedia Gualerzi, a family business in Italy. Embracing digital workflows, they use Oqton Freeform for designing 3D models. Nobel88, their B2B arm, manufactures and trains other O&P companies. Despite early challenges, they now produce diverse medical devices, including spinal braces and prostheses, with Freeform’s help.

A custom spinal brace for scoliosis correction, designed using Freeform from a 3D patient scan and produced with a milling machine.
Sculpting and CAD in one software
Freeform bridges the gap between sculpting and CAD software, essential for O&P 3D design. Initially, Gualerzi tried Blender, Zbrush, and Meshmixer, but they lacked CAD capabilities. He also combined Rhino with Meshmixer or ZBrush, but found Freeform to be the most comprehensive solution.
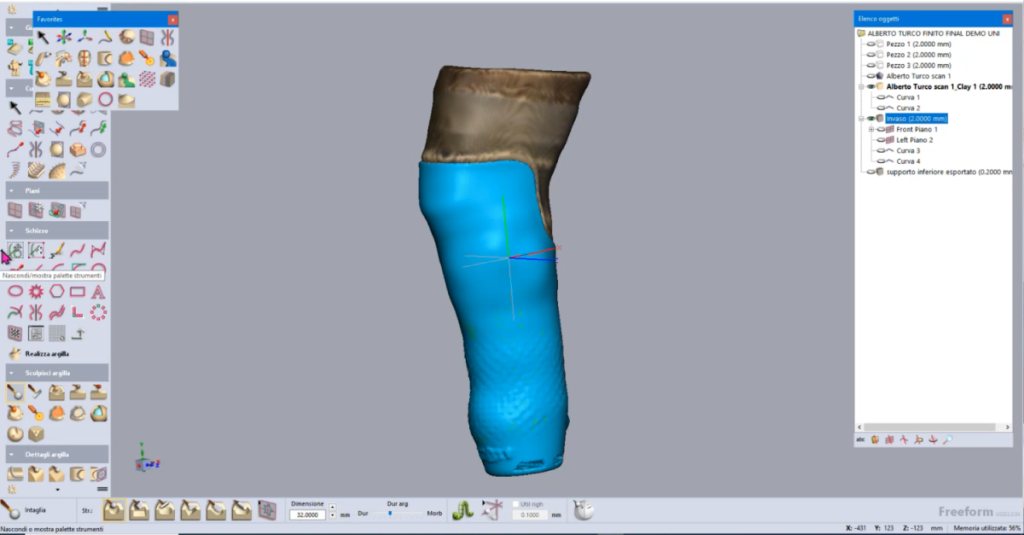
A leg prosthesis was designed using Freeform and 3D-printed on an HP machine with PA12 material. The entire process took under half a workday: 15 minutes for scanning, 45 minutes for design, and a few hours for printing.
The digital advantage
Nobel88 sells Freeform through Teoresi Group and trains CPOs to use it, aiming for widespread adoption in O&P. They advocate digital workflows for increased productivity, allowing CPOs to produce more with tools like 3D scanners, Freeform, and milling machines. To support smaller businesses, Nobel88 developed a compact milling machine compatible with Freeform designs. They believe the future of orthotics involves both 3D printing and milling.
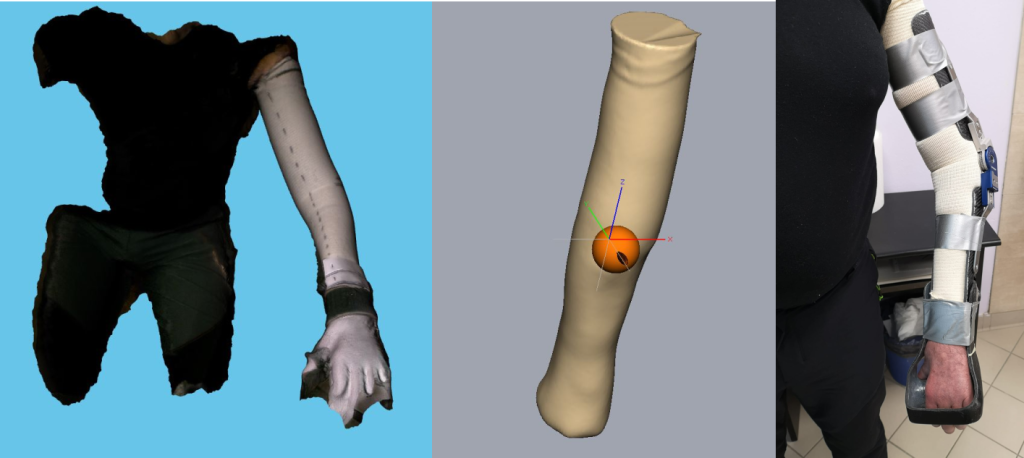
Orthotic for a brachial plexus injury: A 3D scan was processed in Freeform and used to mill a positive model.
Leave A Comment