Radical weight reduction, enhanced performance, and short lead times. These are just a few advantages that drive aerospace companies to adopt 3D printing. But one major challenge is deterring them from fully committing to the technology – the hefty price of mistakes.
The materials alone are so expensive that printing a single part sometimes costs tens of thousands of dollars. Additionally, aerospace parts need to comply with exacting standards where the tolerance for errors is low. Mistakes that would be considered insignificant in other industries are inadmissible in aerospace.
The high cost of printing underscores the need to reduce the likelihood of mistakes and de-risk additive manufacturing. Simulation is part of the solution. With the simulation and compensation tools in Oqton’s 3DXpert software and a simple workflow, you can print parts right in record time and eliminate material waste.
Capturing additive manufacturing expertise
In the infancy of additive manufacturing, the risk of build failure, deformation or overheating was simply something manufacturers needed to accept. With time, experts gained sufficient process knowledge to avoid common pitfalls. Today their experience is captured in simulation tools, enabling users to identify and prevent problems before they occur.
However, not all simulation tools are made equal. If you want to leverage them, you may come up against a few challenges.
The first challenge is software complexity. Simulation tools may require expert knowledge and training to obtain reliable results. A lot of operators struggle to master that learning curve and leverage the software in their work environment. Even if you learn how to use it, you’re more likely to make mistakes if it’s complex.
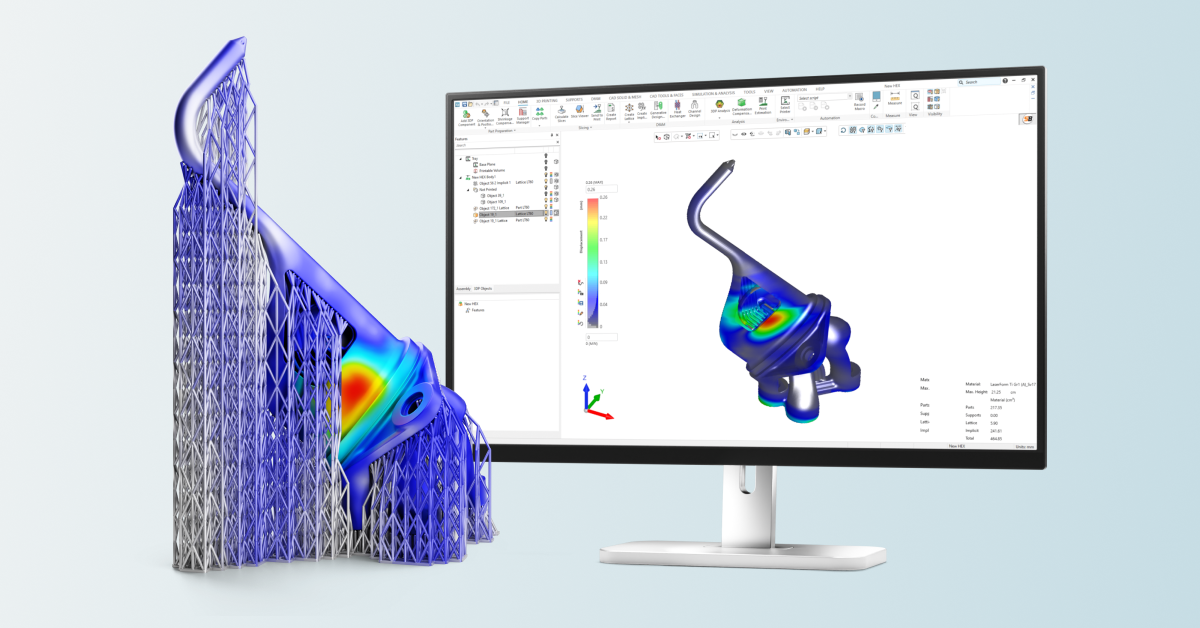
The simulation and compensation tools in 3DXpert enable aerospace companies to print parts correctly in record time.
The second major challenge is time. Significant processing power is required to run a simulation due to complex calculations a computer needs to carry out. As a result, a single simulation can take up to eight hours. Some projects require two or three simulations, which means several days of work are spent just simulating the process.
The third challenge is lack of integration. Many simulation tools are a stand-alone solution separate from 3D printing software. This has important repercussions for workflows. You need to prepare a build, export it as an STL, load it into the simulation tool, simulate, and transfer the data back to the 3D printing software, to carry out the rest of the process or to adjust the build. This back-and-forth significantly slows product development.
The solution is developing software that is simpler, requires less computational power and seamlessly connected with the rest of the printing software. 3DXpert delivers on all these fronts.
The capabilities are sophisticated, but intuitive. The simulation module is more computationally effective and requires less information about the process. The module is part of a comprehensive 3D printing solution for the entire workflow. The process is simpler and the feedback loop is faster. You don’t need to learn how to use a new piece of software, or to leave the software to fix support strategies. Finally, meshes are more accurate being generated directly on the build, and not on meta-data.
With this solution in place, you can implement a simple workflow to reduce the use of material, time and labour.
Simulation-compensation workflow that de-risks additive manufacturing
The workflow consists of a sequence of steps:
- a few fast low-fidelity mechanical simulations
- a high-fidelity simulation
- pre-deformation compensation
- a final, thermal simulation
The first goal is to identify major issues, such as support failure, excessive deformations, or recoater interference. Because these are easy to detect, a low-fidelity, fast mechanical simulation, is ideal. Often, two or three simulations will suffice to identify the issues and fix them. Typical adjustments include increasing total support amount, wall thickness, changing orientation or the support strategy.
The advantage of running a low-fidelity simulation at the beginning is that you can quickly iterate and fix major issues. Once the risk of failure is low, you run a high-fidelity simulation.
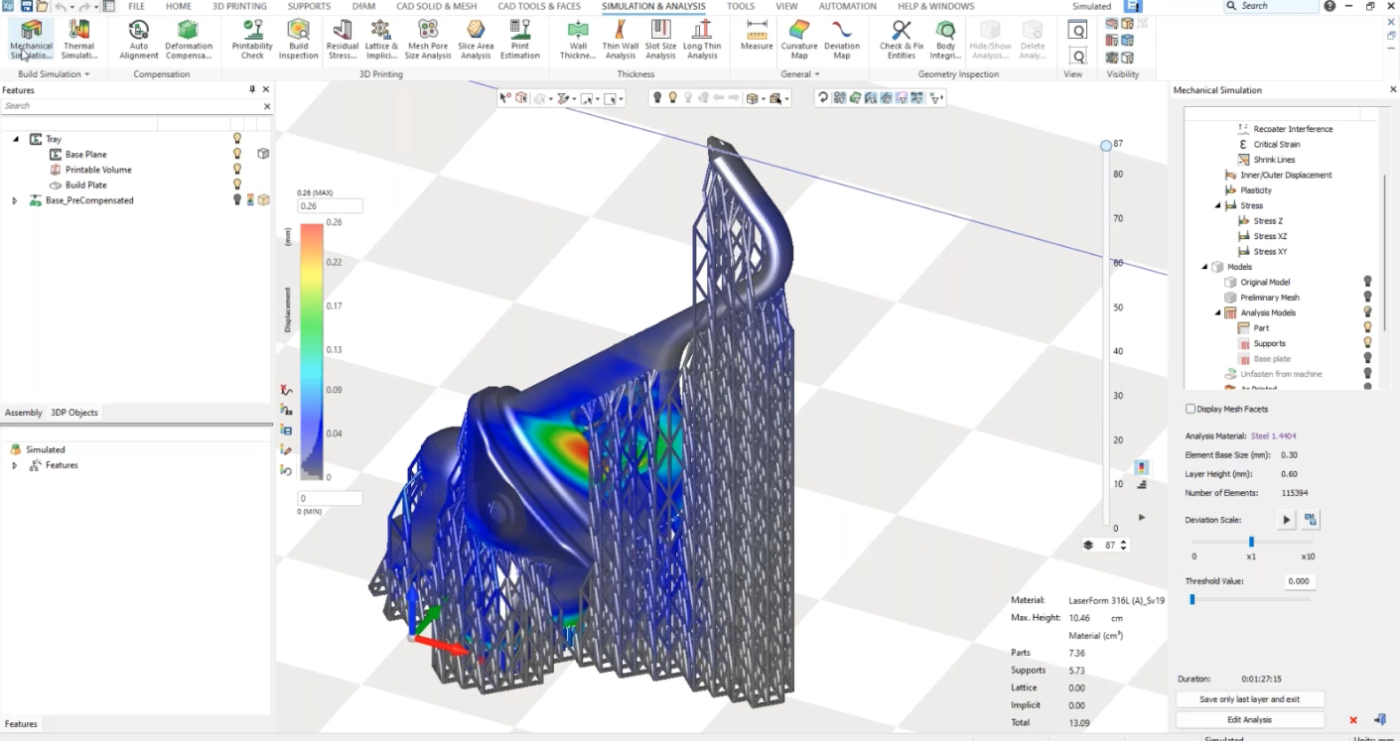
A simulation of an aerospace part in 3DXpert with a heatmap indicating deformations.
This simulation serves as a basis for a pre-deformation compensation, a process which involves changing the part model so the printed part aligns with the expected build. High-fidelity simulation captures the deformations more accurately and yields better compensation results, but it takes anywhere from one to four hours to run.
After adjusting an individual part, it’s time to simulate the build plate. You lay out the build and run a thermal simulation to determine the risk of destabilization. The primary goal is to prevent exposing a part to excess heat, also known as “burning” the part, which degrades its material properties. If thermal stability is confirmed, the part can be sent to the printer.
This simulation-compensation approach results in an accuracy of a higher order. The simulation tool is fast and, on average, reduces the development prints by half, down to two to three, minimizing machine time and material use.
Combining simulation with scan-based compensation and inspection
You can further enhance the quality of the part with two post-printing approaches: scan-based compensation and build inspection.
Scan-based compensation uses three inputs – the CAD model, the compensated model, and an optical 3D scan of the actual print. These are superimposed inside 3D printing software and a new more accurate compensated model is generated.
The final stage of the quality process is build inspection. During this step, pictures are taken of the envelope during printing to capture errors that may have been missed in the simulation and correct the original model.
This approach enables you to consistently produce quality AM parts, maximize the value of the technology and extend the range of its applications.
Additive manufacturing in aerospace
The aerospace industry offers many opportunities for AM, but there are certain pitfalls to avoid. De-risking with simulation is one of several measures that manufacturers are taking to use AM cost-effectively. Contact us about Oqton’s software and how you can incorporate it into your workflow.
Leave A Comment